「必要なものを、必要な時に、必要な量だけ」供給して、効率的に生産するジャストインタイム。耳にしたことはあっても、導入するメリットや必要性については十分理解できていない方も多いでしょう。本記事ではジャストインタイムについて、活用するメリットや導入すべき企業の特徴を踏まえて紹介します。ジャストインタイムを把握するうえで重要な「かんばん方式」や「3原則」にも触れているので、ぜひ最後までご覧ください。
ジャストインタイムとは
ジャストインタイムとはトヨタ自動車が開発・導入した生産管理システムのことです。「必要なものを、必要な時に、必要な量だけ」供給して、効率的に生産するシステムとして知られています。
ジャストインタイムでは、前工程から製品・部品を必要な時に必要な量だけ引き取る「後工程引取方式」を採用しています。後工程引取の大きな特徴は、各製造工程で作業が完了した段階で、次の工程に引き渡されることです。この方式により、どこかの製造ラインに作業が集中して製造が滞ったり、一部の部品を大量に作ってしまうといった在庫の無駄を無くすことができます。前工程は、後工程から指示があった分だけ製品を生産できるので、不要な在庫を抱えにくいのが特徴です。
トヨタのかんばん方式との違い
ジャストインタイムと似た生産方式に「かんばん方式」があります。結論、2つの方式の関係性は「後工程引取方式にかんばん(生産指示標)の仕組みを応用した方式がジャストインタイムである」ことと理解しておきましょう。上述した後工程引取方式をスムーズに行うため、製造に必要な情報をやりとりする納品書のような役目を果たすのが「かんばん」です。
かんばん方式では、発注が入った段階でかんばん(生産指示標)に従って部品の製造・加工などを行い、作業が完了したら、かんばんとともに後工程に部品を引き渡します。後工程はかんばんを受け取った段階で作業を開始し、完了後に次の工程に引き継ぐという流れが繰り返されます。かんばん方式は、ジャストインタイムの基本となる生産方式であることを頭に入れておきましょう。
ジャストインタイムの3原則
ジャストインタイムには3つの原則があり、この原則が守られなければ在庫の無駄を削減できません。ここでは、ジャストインタイムを理解するうえで重要な3原則について解説します。
工程の流れ化
1つ目の原則が、工程内に製品を停滞させず、次の工程に次々とパスする「工程の流れ化」です。製品を停滞させないためには「1つ製品を作るごとにラインに流す」といった工夫が必要だといわれています。
必要数によるタクトタイムの決定
2つ目の原則が、稼働時間を生産必要数で割ったタクトタイムの決定です。タクトタイムとは、製品の必要数に応じて最適な人数の製造ラインを作り、稼働させる時間のことを指します。
稼働時間に対して人員が多い場合は、必要数よりも余分に製品を生産することになり、在庫と時間が無駄になります。これに対して人員が少ない場合は、製品が必要数よりも不足するため欠品リスクが高まります。
時間・在庫の無駄と欠品リスクを防ぐためには、最適なタクトタイムを定める必要があるでしょう。
後工程引取方式
3つ目の原則は、後工程は必要な量・ものを必要な時に前工程から引き取る、後工程引取方式です。すでに説明した通り、前工程は後工程で必要な分だけを生産するので、無駄なく効率的に製品を生産できます。大量生産と欠品リスクを防げる後工程引取方式は、ジャストインタイムの中心となる原則です。
ジャストインタイムを導入するメリット
ジャストインタイムを導入する主なメリットには、在庫やコストの削減が挙げられます。
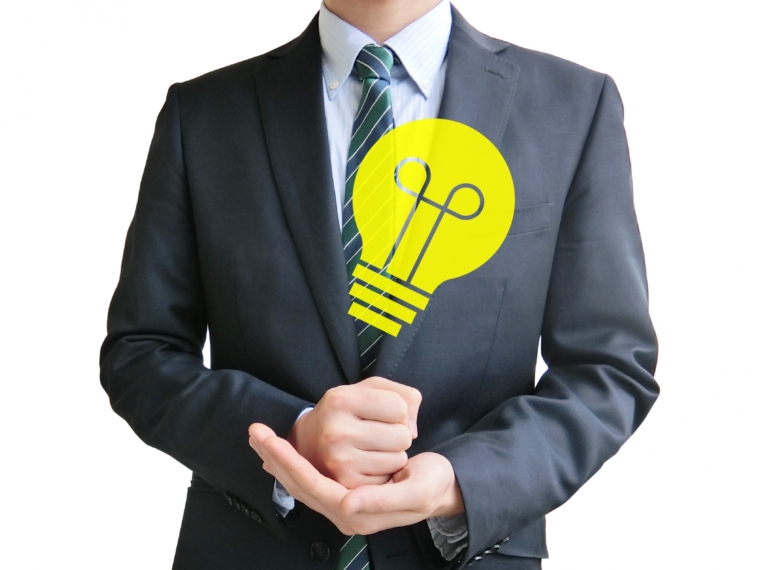
在庫量が減る
ジャストインタイムに取り組めば、必要なものを必要な量だけ必要な時に生産できます。そのため、無駄な在庫の減少につながるでしょう。
また従来は、在庫量が減った影響で生産が遅れてしまうこともありました。ジャストインタイムは後工程から指示があるとすぐに製品を生産するため、発注から納品に至るまでの時間を短縮できます。
コストを削減できる
コストが削減できる点も、ジャストインタイムを導入するメリットです。在庫を抱えている場合、主に以下の2つの費用がかかります。
- 在庫管理費用: その製品の運搬やメンテナンスにかかる費用
- 余分な製品を生産する際にかかる費用:原材料費や人件費など
上記のように、在庫を抱えるとさまざまなコストがかかります。ジャストインタイムを導入すれば抱える在庫が減るため、コストの削減につながるでしょう。
ジャストインタイムの問題点
在庫やコスト削減におけるメリットが期待できるジャストインタイム。しかし、問題点があるのも事実です。ジャストインタイムのデメリットとなりうる点も把握して、自社に取り入れるべきか判断しましょう。
在庫切れのリスクがある
ジャストインタイムの導入には、在庫切れのリスクがあることを頭に入れておきましょう。特に受注量が急に増えた場合は適応が難しいため、注意が必要です。また原材料の仕入れ先でトラブルが発生し、生産がストップした場合も在庫切れの原因になります。
下請けいじめのような状態を招きやすい
ジャストインタイムに取り組んでいる親会社は、過剰生産を防ぎつつ欠品リスクを回避するため、下請けメーカーに対してできる限り短い納期かつ少量の納品を求める傾向にあります。
しかし多くの下請けメーカーは、設備や人材など生産にかかわるリソースが限られています。納期遅れを防ぐためにも、リードタイムが長いものは早めに生産して在庫として保管しなくてはなりません。
親会社が不要な在庫を抱えるリスクを縮小することで、下請けメーカーにその分の負担が回ってきます。ジャストインタイムは、発注方法によっては下請け会社を苦しめる可能性があることを忘れてはいけません。
ある程度の導入費用が必要
ジャストインタイムの仕組みを確立するためには、かんばん方式を構築する際などの費用がかかります。
トヨタのように、ジャストインタイムを導入するための仕組みがある程度整っている場合であれば、莫大なコストはかからないでしょう。しかし、ほとんど設備のない中小企業が一から仕組みを構築するには、相応の費用がかかることを覚えておきましょう。
ジャストインタイムを導入すべき企業の特徴
ここでは、ジャストインタイムを導入すべき企業の特徴を2つ紹介します。ここで紹介する2つの特徴に当てはまった企業は、導入を検討してみましょう。
商品の需要が平準化されている
商品の需要が平準化されていなければ、ジャストインタイムは導入すべきではありません。例えば「明日はこの製品を200個生産して欲しいけれど、明後日は10個で大丈夫」など、日によって生産数が異なる際は、前章で紹介した下請けへの負担につながりかねません。
親会社と下請けメーカー双方がメリットを享受するのが、ジャストインタイムのあるべき姿です。日ごとに生産要求数が異なり下請け会社に迷惑がかかる状況であれば、導入すべきではありません。対して、商品の需要が平準化されているのであれば、導入を検討してもよいでしょう。
部品を安定的に供給できる
安定的に部品を供給できるのであれば、導入を検討する余地があります。ジャストインタイムは在庫を持たないため、仕入れ先でトラブルが発生して生産が止まると、在庫切れになる可能性があります。顧客満足度の低下や機会損失にもつながるため、部品の安定的な供給を意識しながら在庫切れを避けなければなりません。
リスク回避のために複数の会社から部品を供給している企業であれば、導入を前向きに検討してもよいでしょう。
まとめ
在庫やコストの削減が期待できるジャストインタイム。しかし同時に在庫切れのリスクや、下請けいじめといった問題点を抱えていることを頭に入れておく必要があります。
ジャストインタイムを導入すべきは、商品の需要が平準化されていて、部品を安定的に供給できる企業です。ジャストインタイムの仕組みを構築するコストを分析しながら、導入を検討しましょう。